
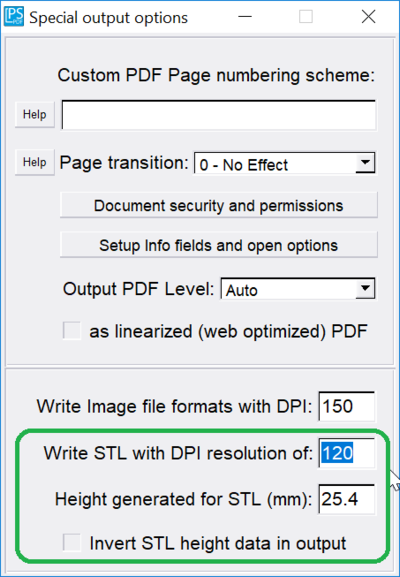
From the Part menu, choose “Create shape from mesh.”.From the toolbar dropdown menu, choose Part.However, you should still try the next steps in case you get lucky. If clicking the Repair button for any other option makes your mesh look terrible, you’re likely out of luck.If clicking the Repair button for “Folds on Surface” makes your mesh look terrible, you can skip that one.One by one, go down the list, clicking Analyze and then Repair if the analysis finds any problems.Select the mesh from the dropdown at the top of the Evaluate & Repair pane.Open the Evaluate & Repair mesh tool (Meshes menu > Analyze > Evaluate & Repair mesh).From the dropdown menu in the top toolbar, choose Mesh design.Import your STL file (File menu > Import > select your STL file).Our conversion tool of choice is FreeCAD because it’s free, relatively simple to use, and does a good job of converting STL files to usable solid models.
#CONVERTING STEP TO STL DOWNLOAD#
That being said, if you have no other option, it’s definitely worth a shot! STEP 1: DOWNLOAD A CONVERSION TOOL If your STL file is of the second type, you won’t be able to convert it.
#CONVERTING STEP TO STL FULL#
Others are extremely complex, full of holes and have many self-intersections, and will cause the crash of the conversion program. Some of them are low-complexity, watertight, and can be easily converted. Select the Model Workspace and then to convert the mesh to a solid body all you’ll have to do is right click on the mesh and select “Mesh to BRep.” You’ll then see in the dialogue box that you can have it create a new body or a new component.Disclaimer: STL files span a wide range. What confuses A LOT of Fusion 360 users is that you’ll actually need to be back in the Model Workspace in order to convert a model.
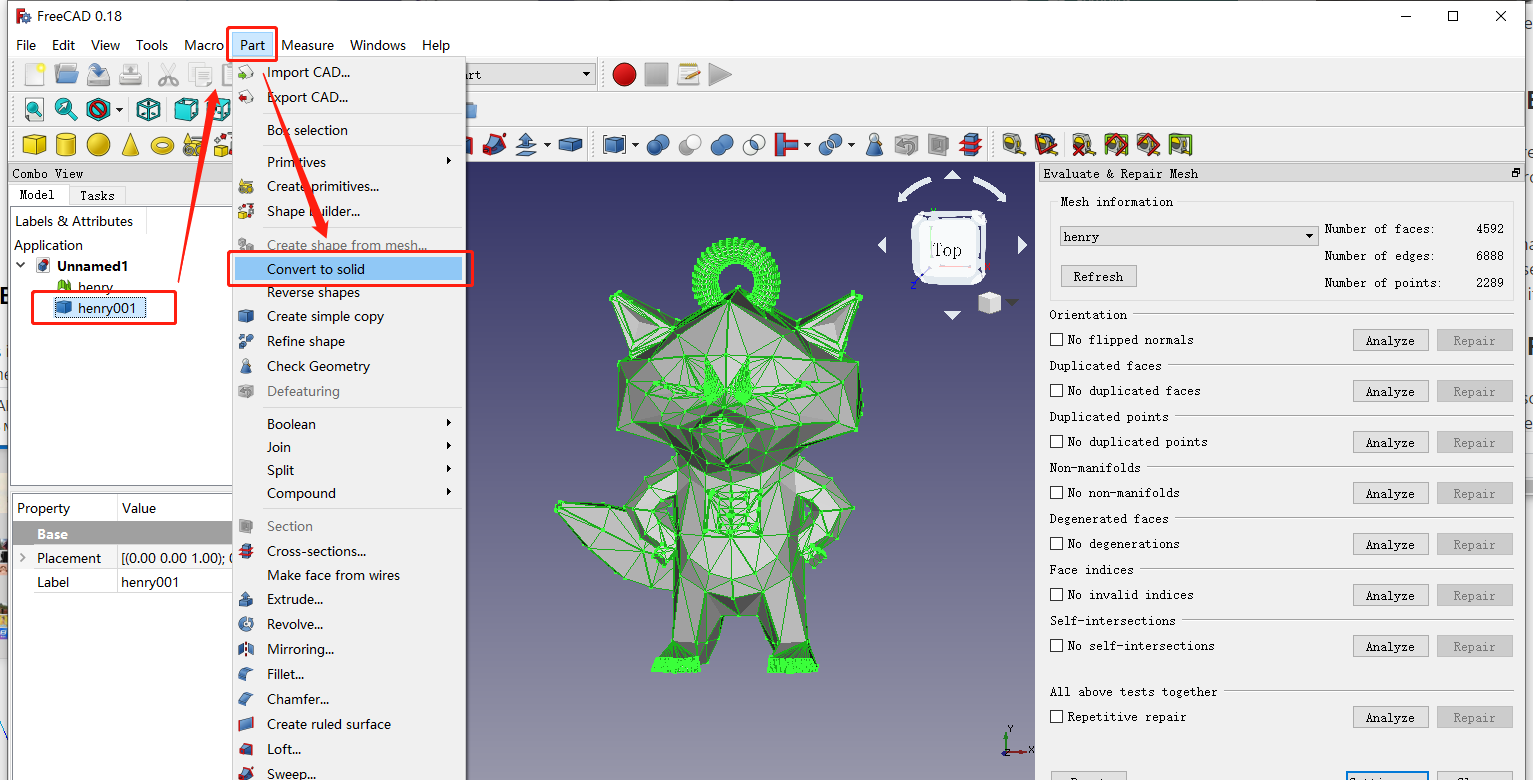
Under the display settings select “visual style,” and then select “shaded with visible edges only.” You’ll see that if you zoom in you can now see all of the vertices, edges, and faces that make up the mesh model (like I discussed above). Now if you go back to the workspace selection menu you’ll see that you can change to the Mesh Workspace.Īt this point, I also recommend changing the visual style so it’s a bit easier to see all the triangles that make up the mesh. You’ll have to turn off the design history by right-clicking on the file in the browser and select “Do Not Capture Design History” and click the continue button to confirm. If you go to the workspaces menu and still can’t see the Mesh Workspace, it’s likely because of the design history. Lastly, be sure to click “okay” to confirm any orientation changes that you’ve made. If your file is floating in space for some reason, you can hit “move to ground” to move it to the XZ or XY plane, depending on how your orientation is set up. You can also hit “center” to move it to the center origin. If I wanted the top of the phone stand to be the top of my orientation in the viewcube I could either drag the sliders around or I could select the “flip-up direction” in the insert mesh dialogue box. Changing Orientation of a Mesh File in Fusion 360 You’ll see that before you can work on the file it allows you to change the orientation.Ģ. Select “insert mesh” from the dropdown list. The second way to insert a mesh file is to simply go to the insert menu. Note: Click here for the phone stand STL file used in this demo. Once the file has been successfully uploaded, double-click on the file to open it. Then, If you select the file you can upload it. The first way would be to open up the data panel and click the blue upload button. There are two ways that you can import a mesh file into Fusion 360. The first thing you’ll have to do is import it into Fusion 360. For this demo, I’m going to use this downloaded phone stand Thingiverse file. stl files from and they want to modify them to fit their own needs or they simply want to customize them with their name or logo.
